Throttle
A throttle is the mechanism by which fluid flow is managed by constriction or obstruction.
An engine's power can be increased or decreased by the restriction of inlet gases (i.e., by the use of a throttle), but usually decreased. The term throttle has come to refer, informally and incorrectly, to any mechanism by which the power or speed of an engine is regulated. What is often termed a throttle (in an aviation context) is more correctly called a thrust lever, particularly for jet engine powered aircraft. For a steam engine, the steam valve that sets the engine speed/power is often known as a regulator.
Internal combustion engines
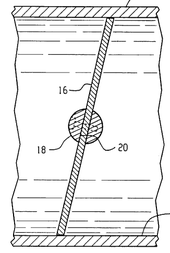
In a petrol/gasoline internal combustion engine, the throttle is a valve that directly regulates the amount of air entering the engine, indirectly controlling the charge (fuel + air) burned on each cycle due to the fuel-injector or carburetor maintaining a relatively constant fuel/air ratio. In a motor vehicle the control used by the driver to regulate power is sometimes called the throttle pedal, as it controls the throttle opening, although "accelerator pedal" is more accurate, since not all vehicles have throttles. A diesel engine does not have a throttle except there is a throttle valve on the newer diesel engines which is generally referred to as air management valves. Air management valves can be with or without integrated control electronics. Air management valves throttle the intake air in the intake air system of diesel engines via electromotive means in order to achieve precision controlled exhaust gas recirculation and prevent the inconvenient shaking that would otherwise occur when the engine is switched off. [1] The power level of a diesel is controlled by regulating the fuel flow into the engine, thus "throttle" and "gas pedal" are both inaccurate terms when applied to any modern computerized engine, diesel or not. Both types (gas and diesel) are now true throttle- by- wire computerized systems with the main difference being that in gasoline engines, the throttle position ultimately controls the amount of air getting into the engine with the computer supplying the fuel via the fuel injectors; whereas in a diesel the throttle position really only informs the computer to supply the amount of fuel via the injectors and in some newer models the actual diesel fuel pressure.[2]
The throttle is typically a butterfly valve. In a fuel-injected engine, the throttle valve is placed on the entrance of the intake manifold, or housed in the throttle body. In a carbureted engine, it is found in the carburetor.
When a throttle is wide open, the intake manifold is usually at ambient atmospheric pressure. When the throttle is partially closed, a manifold vacuum develops as the intake drops below ambient pressure.
Usually, the throttle valve is controlled with a throttle pedal or lever via a direct mechanical linkage. In vehicles with electronic throttle control, the manual throttle control sends a signal to the Engine Control Unit (ECU), which then directly controls the position of the throttle valve. This means that the operator does not have direct control over the throttle valve; the ECU can finely control the valve in order to reduce emissions or maximize performance.
In a reciprocating-engine aircraft, the throttle control is usually a hand-operated lever or knob. It controls the engine power output, which may or may not reflect in a change of RPM, depending on the propeller installation (fixed-pitch or constant speed).[3]
The power output of a diesel engine is controlled by regulating the quantity of fuel that is injected into the cylinder. Because the engines do not need to control air volumes, they lack a butterfly valve in the intake tract. An exception to this generalization is newer diesel engines meeting stricter emissions standards, where a throttle is used to generate intake manifold vacuum, thereby allowing the introduction of exhaust gas (see EGR) to lower combustion temperatures and thereby minimize NOx production.
Some modern internal combustion engines (such as some BMW engines) do not use a traditional throttle, instead relying on their variable intake valve timing system to regulate the airflow into the cylinders, although the end result is the same, albeit with less pumping losses.
Throttle body
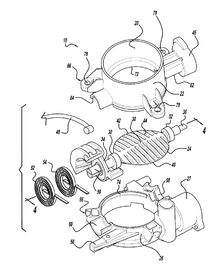
In fuel injected engines, the throttle body is the part of the air intake system that controls the amount of air flowing into the engine, in response to driver accelerator pedal input in the main. The throttle body is usually located between the air filter box and the intake manifold, and it is usually attached to, or near, the mass airflow sensor.
The largest piece inside the throttle body is the throttle plate, which is a butterfly valve that regulates the airflow.
On many cars, the accelerator pedal motion is communicated via the throttle cable, to activate the throttle linkages, which move the throttle plate. In cars with electronic throttle control (also known as "drive-by-wire"), an electric motor controls the throttle linkages and the accelerator pedal connects not to the throttle body, but to a sensor, which sends the pedal position to the Engine Control Unit (ECU). The ECU determines the throttle opening based on accelerator pedal position and inputs from other engine sensors.
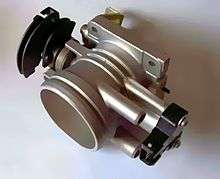
When the driver presses on the accelerator pedal, the throttle plate rotates within the throttle body, opening the throttle passage to allow more air into the intake manifold. Usually an airflow sensor measures this change and communicates with the ECU. The ECU then increases the amount of fuel being sent to the fuel injectors in order to obtain the desired air-fuel ratio. Often a throttle position sensor (TPS) is connected to the shaft of the throttle plate to provide the ECU with information on whether the throttle is in the idle position, wide-open throttle (WOT) position, or somewhere in between these extremes.
Throttle bodies may also contain valves and adjustments to control the minimum airflow during idle. Even in those units that are not "drive-by-wire", there will often be a small solenoid driven valve, the Idle Air Control Valve (IACV), that the ECU uses to control the amount of air that can bypass the main throttle opening to allow the engine to idle when the throttle is closed.
The most basic carbureted engines, such as single cylinder Briggs & Stratton lawn-mower engines, feature a single small throttle plate over a basic carburetor with a single venturi. The throttle is either open or closed (although there is always a small hole or other bypass to allow a small amount of air to flow through so the engine can idle when the throttle is closed), or some intermediate position. Since air velocity is crucial to the functioning of a carburetor, to keep average air velocity up, larger engines require more complex carburetors with multiple small venturis, typically two or four (these venturis are commonly called "barrels). A typical "2-barrel" carburetor uses a single oval or rectangular throttle plate, and works similarly to a single venturi carburetor, but with two small openings instead of one. A 4-venturi carburetor has two pairs of venturis, each pair regulated by a single oval or rectangular throttle plate. Under normal operation, only one throttle plate (the "primary") opens when the accelerator pedal is pressed, allowing more air into the engine, but keeping overall airflow velocity through the carburetor high (thus improving efficiency). The "secondary" throttle is operated either mechanically when the primary plate is opened past a certain amount, or via engine vacuum, influenced by the position of the accelerator pedal and engine load, allowing for greater air flow into the engine at high RPM and load and better efficiency at low RPM's. Multiple 2-venturi or 4-venturi carburetors can be used simultaneously in situations where maximum engine power is of priority.
Most fuel injected cars have a single throttle, contained in a throttle body. Vehicles can sometimes employ more than one throttle body, connected by linkages to operate simultaneously, which improves throttle response and allows a straighter path for the airflow to the cylinder head, as well as for equal-distance intake runners of short length, difficult to achieve when all the runners have to travel to certain location to connect to a singe throttle body, at the cost of greater complexity and packaging issues. At the extreme, higher-performance cars like the E92 BMW M3 and Ferraris, and high-performance motorcycles like the Yamaha R6, can use a separate throttle body for each cylinder, often called "individual throttle bodies" or ITBs. Although rare in production vehicles, these are common equipment on many racing cars and modified street vehicles. This practice hearkens back to the days when many high performance cars were given one, small, single-venturi carburetor for each cylinder or pair of cylinders (i.e. Weber, SU carburetors), each one with their own small throttle plate inside. In a carburetor, the smaller throttle opening also allowed for more precise and fast carburetor response, as well as better atomization of the fuel when running at low engine speeds.
A throttle body is somewhat analogous to the carburetor in a non-injected engine, although it is important to remember that a throttle body is not the same thing as a throttle, and that carbureted engines have throttles as well. A throttle body simply supplies a convenient place to mount a throttle in the absence of a carburetor venturi. Carburetors are an older technology, which mechanically modulate the amount of air flow (with an internal throttle plate) and combine air and fuel together (venturi). Cars with fuel injection don't need a mechanical device to meter the fuel flow, since that duty is taken over by injectors in the intake pathways coupled with electronic sensors and computers which calculate how much fuel is needed. However, they do still need a throttle to control the airflow into the engine. The simplest way to do this is to simply remove the carburetor unit, and bolt a simple unit containing a throttle body and fuel injectors on instead. This is known as throttle body injection (called TBI by General Motors and CFI by Ford), and it allows an older engine design to be converted from carburetor to fuel injection without significantly altering the intake manifold design. More complex later designs use intake manifolds, and even cylinder heads, specially designed for the inclusion of injectors.
Other engines
Steam locomotives normally have the throttle (North American English) or regulator (British English) in a characteristic steam dome at the top of the boiler (although not all boilers feature these). The additional height afforded by the dome helps to avoid any liquid (e.g. from bubbles on the surface of the boiler water) being drawn into the throttle valve, which could damage it, or lead to priming. The throttle is basically a poppet valve, or series of poppet valves which open in sequence to regulate the amount of stream admitted to the steam chests over the pistons. It is used in conjunction with the reversing lever to start, stop and to control the locomotive's power although, during steady-state running of most locomotives, it is preferable to leave the throttle wide open and to control the power by varying the steam cut-off point (which is done with the reversing lever), as this is more efficient. A steam locomotive throttle valve poses a difficult design challenge as it must be opened and closed using hand effort against the considerable pressure (typically 250psi) of boiler steam (one of the primary reasons for later multiple-sequential valves...it is far easier to open a small poppet valve against the pressure differential, and open the others once pressure begins to equalize than to open a single large valve, especially as steam pressures eventually exceeded 200 or even 300 psi. Examples include the balanced "double beat" type used on Gresley A3 Pacifics.
Throttling of a rocket engine means varying the thrust level in-flight. This is not always a requirement; in fact, the thrust of a solid-fuel rocket is not controllable after ignition. However, liquid-propellant rockets can be throttled by means of valves which regulate the flow of fuel and oxidizer to the combustion chamber. Hybrid rocket engines, such as the one used in Space Ship One, use solid fuel with a liquid oxidizer, and therefore can be throttled. Throttling tends to be required more for powered landings, and launch into space using a single main stage (such as the Space Shuttle), than for launch with multistage rockets. They are also useful in situations where the airspeed of the vehicle must be limited due to aerodynamic stress in the denser atmosphere at lower levels (i.e. the Space Shuttle)
In a jet engine, thrust is controlled by changing the amount of fuel flowing into the combustion chamber, similar to a diesel engine. Thus, the name "throttle" is a misnomer (more accurately known as a "thrust lever", as in most Airbus and Boeing aircraft). This is chiefly because "throttle" is a legacy of traditional gasoline aircraft engines.[4]
See also
References
- ↑ http://www.my-cardictionary.com/electronics/throttle-valve.html
- ↑ "Automotive Technology A Systems Approach" publisher Delmar, Cengage Learning 2016
- ↑ "Chapter 6: Aircraft Systems" (PDF). Pilot's Handbook of Aeronautical Knowledge. Federal Aviation Administration. 2008. Retrieved 2009-02-09.
- ↑ "CEO of the Cockpit #84: Terms of Up-Gearment". Avweb.com. 2008-06-30. Retrieved 2009-09-10.
External links
![]() |
Look up throttle in Wiktionary, the free dictionary. |