Rosendale cement
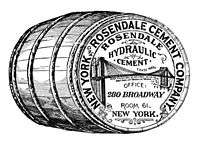
Rosendale cement generally refers to a type of natural cement that was produced in and around Rosendale, New York, from argillaceous limestone, but is a term that has had different definitions at different times.[1] The fast-setting Rosendale natural cement mortars proved to be more efficient than the mortars based on lime and sand. Because of its reputation, Rosendale cement has also been used as both a trade name and as a generic term referring to natural hydraulic cements produced elsewhere. It was used in the construction of many of the United States' most important landmarks, including the Brooklyn Bridge, the pedestal of the Statue of Liberty, Federal Hall National Memorial, and one of the wings of the United States Capitol building.
Natural cement is produced in a process that begins with the calcination of crushed carbonate sedimentary rocks in kilns. The resulting clinker is ground into a fine powder before being shipped to market. Historically, this natural cement product was packaged in paper-lined wooden barrels or heavy canvas bags. Rosendale natural cement from the Rosendale area was produced from dolostone extracted from the Rosendale and Whiteport members of the Late Silurian Rondout Formation. The natural levels of magnesium and clay in the dolostone from the Rondout formation are ideally suited for cement production and required none of the chemical additives characteristic of modern Portland cement production.
While Rosendale cement was extremely popular for the foundation of buildings (e.g. Statue of Liberty, Capitol Building, Brooklyn Bridge) and lining of water pipes, its long curing time of at least one month made it unpopular after World War I in the construction of highways and bridges, and many states and construction firms turned to Portland cement. Because of the switch to Portland cement, by the end of the 1920s, only one of the 15 Rosendale cement companies had survived. In the early 1930s, it was discovered that Portland cement, with a faster curing time, was not as durable, especially for highways. As a result, some states stopped building highways and roads with cement. Engineer Bertrain H. Wait, whose company had worked on the construction of the New York City's Catskill Aqueduct, was impressed with the durability of Rosendale cement and devised a blend of Rosendale and synthetic cements which had the good attributes of both: durable and a much faster curing time. Mr. Wait convinced the New York Commissioner of Highways to construct near New Paltz, New York, an experimental section of highway using one sack of Rosendale to six sacks of synthetic cement. It proved a success, and for decades the Rosendale-synthetic cement blend was common in highway and bridge construction.[2]
Many of the original cement plants in the Rosendale area are preserved in the Snyder Estate Natural Cement Historic District.
See also
References
- ↑ Werner, Dietrich; Burmeister, Kurtis (2007). "An Overview of the History and Economic Geology of the Natural Cement Industry at Rosendale, Ulster County, New York". Journal of ASTM International. 4 (6). doi:10.1520/JAI100672. Retrieved 24 October 2015.
- ↑ "Natural Cement Comes Back", October 1941, Popular Science.