SU Carburettor
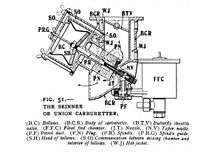
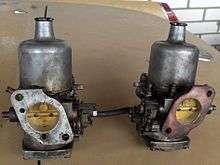
SU carburettors are a brand of carburettor of the constant depression type. The design remained in quantity production for much of the twentieth century.
The S.U. Carburetter Company Limited also manufactured dual-choke updraught carburettors for aero-engines such as the Rolls-Royce Merlin and Rolls-Royce Griffon.[1]
Invention and development
Herbert Skinner (1872-1931), pioneer motorist and an active participant in the development of the petrol engine,[2] invented his Union carburettor in 1904.[3] His much younger brother Carl (Thomas Carlisle) Skinner (1882-1958) also a motoring enthusiast had joined the Farman Automobile Co in London in 1899.[4] He helped Herbert to develop the carburettor.[4] Herbert's son could remember his mother sewing the first leather bellows.[5] It would be given on loan to The Science Museum, South Kensington in 1934.[3][6] In 1905 Herbert applied for a patent[5] which was granted in early 1906.[7] Later Carl sold his interest in footwear business Lilley & Skinner and became a partner in G Wailes & Co of Euston Road, London, manufacturers of their carburettor.[4] Herbert continued to develop and patent improvements through to the 1920s including the replacement of the leather bellows by a brass piston though he was a full-time director and divisional manager of Lilley & Skinner.[3][8][9]
S. U. Company Limited
S. U. Company Limited —Skinner-Union—[10][11][12][13] was incorporated in August 1910[note 1] to acquire Herbert's carburettor inventions and it began manufacture[2] of the carburettors in a factory at Prince of Wales Road, Kentish Town in North London.[14] Sales were slow. Following the outbreak of war in 1914 carburettor production nearly stopped with the factory making machine gun parts and some aircraft carburettors. With peace in 1918 production resumed but sales remained slow and the company was not profitable so Carl Skinner approached his customer, W. R. Morris, and managed to sell him the business.[11] Carl Skinner (T C Skinner) became a director of Morris's privately held empire and remained managing director of S.U. until he retired in 1948 aged 65.[4] Production was moved to the W R Morris owned Wolseley factory at Adderley Park, Birmingham. In 1936 W R Morris sold many of his privately held businesses including S. U. to his listed company, Morris Motors.[15][16]
The S. U. Carburetter Company Limited
Manufacture continued, now by The S. U. Carburetter Company Limited which was incorporated 15 September 1936[17] part of the Morris Organization, later known as the Nuffield Organization.[15] The S. U. Carburetter Company Limited of 1936[17] was voluntarily liquidated in December 1994.
In 1996 the name and rights were acquired by Burlen Fuel Systems Limited of Salisbury[14] which incorporated an entirely new company with the name The S.U. Carburetter Company Limited[18] which continues to manufacture carburettors, pumps and components mainly for the classic car market.
Applications
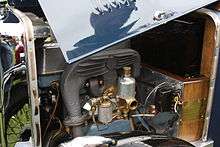
S.U. carburettors were widely used not only in Morris's Morris and MG products but Rolls-Royce, Bentley, Rover, Riley, Turner, Austin, Jaguar, Triumph and Swedish Volvo, Saab 99 automobiles for much of the twentieth century. They were also fitted to aircraft engines including the Rolls-Royce Merlin.
They remained on production cars through to 1993 in the Mini and the Maestro by which time the company had become part of the Rover Group.
Hitachi also built carburettors based on the SU design which were used on the Datsun 240Z, Datsun 260Z and other Datsun Cars. While these appear the same, only their needles are interchangeable.
Operating principle
.jpg)
.jpg)
SU carburettors featured a variable venturi controlled by a piston. This piston has a tapered, conical metering rod (usually referred to as a "needle") that fits inside an orifice ("jet") which admits fuel into the airstream passing through the carburettor. Since the needle is tapered, as it rises and falls it opens and closes the opening in the jet, regulating the passage of fuel, so the movement of the piston controls the amount of fuel delivered, depending on engine demand.
The flow of air through the venturi creates a reduced static pressure in the venturi. This pressure drop is communicated to the upper side of the piston via an air passage. The underside of the piston is open to atmospheric pressure. The difference in pressure between the two sides of the piston lifts the piston. Opposing this are the weight of the piston and the force of a spring that is compressed by the piston rising. Because the spring is operating over a very small part of its possible range of extension, its force is approximately constant. Under steady state conditions the upwards and downwards forces on the piston are equal and opposite, and the piston does not move.
If the airflow into the engine is increased - by opening the throttle plate (usually referred to as the "butterfly"), or by allowing the engine revs to rise with the throttle plate at a constant setting - the pressure drop in the venturi increases, the pressure above the piston falls, and the piston is sucked upwards, increasing the size of the venturi, until the pressure drop in the venturi returns to its nominal level. Similarly if the airflow into the engine is reduced, the piston will fall. The result is that the pressure drop in the venturi remains the same regardless of the speed of the airflow - hence the name "constant depression" for carburettors operating on this principle - but the piston rises and falls according to the speed of the airflow.
Since the position of the piston controls the position of the needle in the jet and thus the open area of the jet, while the depression in the venturi sucking fuel out of the jet remains constant, the rate of fuel delivery is always a definite function of the rate of air delivery. The precise nature of the function is determined by the profile of the needle. With appropriate selection of the needle, the fuel delivery can be matched much more closely to the demands of the engine than is possible with the more common fixed-venturi carburettor, an inherently inaccurate device whose design must incorporate many complex fudges to obtain usable accuracy of fuelling. The well-controlled conditions under which the jet is operating also make it possible to obtain good and consistent atomisation of the fuel under all operating conditions.
This self-adjusting nature makes the selection of the maximum venturi diameter (colloquially, but inaccurately, referred to as "choke size") much less critical than with a fixed-venturi carburettor.
To prevent erratic and sudden movements of the piston it is damped by light oil (20W Grade) in a dashpot, which requires periodic replenishment. The damping is asymmetrical: it heavily resists upwards movement of the piston. This serves as the equivalent of an "accelerator pump" on traditional carburettors by temporarily increasing the speed of air through the venturi, thus increasing the richness of the mixture.
SU carburettors do not have a conventional choke flap, which in a fixed-jet carburettor enriches the mixture for starting the engine from cold by restricting the air supply upstream of the venturi. Instead a mechanism lowers the jet assembly, which has the same effect as the needle rising in normal operation - namely increasing the supply of fuel so that the carburettor will now deliver an enriched mixture at all engine speeds and throttle positions. The 'choke' mechanism on an SU carburettor usually also incorporates a system for holding the throttle plate slightly open to raise the engine's idling speed and prevent stalling at low speeds due to the rich mixture.
The beauty of the SU lies in its simplicity and lack of multiple jets and ease of adjustment. Adjustment is accomplished by altering the starting position of the jet relative to the needle on a fine screw (26TPI for most pre-HIF versions). At first sight, the principle appears to bear a similarity to that of the slide carburettor, which was previously used on many motorcycles. The slide carburettor has the same piston and main needle as an SU carburettor, however the piston/needle position is directly actuated by a physical connection to the throttle cable rather than indirectly by venturi airflow as with an SU carburettor. This piston actuation difference is the significant distinction between a slide and an SU carburettor. The piston in a slide carburettor is controlled by the operator's demands rather than the demands of the engine. This means that the metering of the fuel can be inaccurate unless the vehicle is travelling at a constant speed at a constant throttle setting - conditions rarely encountered except on motorways. This inaccuracy results in fuel waste, particularly as the carburettor must be set slightly rich to avoid a lean condition (which can cause engine damage). For this reason Japanese motorcycle manufacturers ceased to fit slide carbs and substituted constant-depression carbs, which are essentially miniature SUs. It is also possible - indeed, easy - to retrofit an SU carburettor to a bike that was originally manufactured with a slide carburettor, and obtain improved fuel economy and more tractable low-speed behaviour.
One of the downsides of the constant depression carburettor is in high performance applications. Since it relies on restricting air flow in order to produce enrichment during acceleration, the throttle response lacks punch. By contrast, the fixed choke design adds extra fuel under these conditions using its accelerator pump.
SU carburettor types
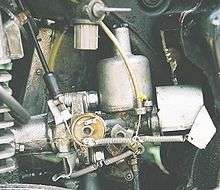
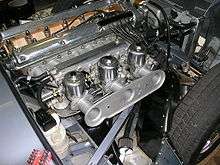
SU carburettors were supplied in several throat sizes in both Imperial (inch) and metric (millimetre) measurement.
The carburettor identification is made by letter prefix which indicates the float type:
- "H": introduced in 1937 in which the float bowl has an arm cast into its base, which mounts to the bottom of the carburetor with a hollow bolt or banjo fitting. Fuel passes through the arm into the carburetor body. The bolt attaches to the carburetor body just behind the main jet assembly.
- "HD": introduced in 1954 with the float bowl mounted with its arm fastening directly below, and concentric with, the main jet. The arm has a flange that fastens with 4 screws to the bottom of the carburetor, and sealed with a rubber diaphragm integral with the main jet.
- "HS": introduced in 1958 with the float bowl rigidly mounted to the carburetor body, but fuel is transferred by a separate external flexible line.
- "HIF": (1982) the float bowl is horizontal and integral (hence the name).
- "HV" (1929), "OM" and "KIF" types also exist but were less commonly employed.[19]
The Imperial sizes include 1-1/8", 1-1/4", 1-1/2", 1-3/4", 1-7/8", and 2", although not every type (H, HD, HS, HIF) was offered in every size.
There were also H models made in 2-1/4" and 2-1/2", now obsolete. Special purpose-built carburetors (Norman) were made as large as 3".
To determine the throat size from the serial number: If the final number (after one, two or three letters, beginning with H) has 1 digit, multiply this number by 1/8", then add 1". For example, if the serial number is HS6, the final number is 6: 6/8 = 3/4", add 1, total is 1-3/4", etc.
If the final number has 2 digits, it is the throat size in mm. For example, if the serial number is HIF38, the final number is 38, size is 38 mm etc.
SU fuel pumps
In 1929 SU introduced the Petrolift electric fuel pump which could be fitted as a substitute for the vacuum type pumps common at the time. This was superseded in 1932 by the L type fuel pump which used a solenoid to operate a diaphragm pump.
See also
Notes
- ↑ S. U. Company Limited, 386—388 Euston Road, N.W. Capital £5,000 in £1 shares. Formed to acquire from G. H. Skinner certain inventions relating to carburettors for motorcars &c
New Companies Registered. Private Companies. The Automotor Journal, 24 September 1910
References
As of this edit, this article uses content from PESWiki, a source licensed under the terms of the GNU Free Documentation License which was imported into Wikipedia before November 2008 and is therefore validly licensed for use on Wikipedia. All relevant terms must be followed. The original article was at "PowerPedia:Carburetor".
- ↑ The Two Rs Flight magazine, p 577, 7 May 1954
- 1 2 Obituary. Mr. G. H. Skinner. The Times, Wednesday, Jan 06, 1932; pg. 12; Issue 46023
- 1 2 3 E A Forward, Handbook of the Collections illustrating Land Transport, II. Mechanical Road Vehicles, Science Museum South Kensington, 1936
- 1 2 3 4 Obituary. Mr. Thomas C. Skinner The Times, Saturday, Nov 15, 1958; pg. 10; Issue 54309
- 1 2 H. Jones: Herbert Wakefield Banks Skinner. 1900-1960. Biographical Memoirs of Fellows of the Royal Society, Vol.6, (Nov. 1960), pp.259-268, publisher: The Royal Society
- ↑ The Science Museum's (1965) carburettor, sectioned
- ↑ 3257 G H Skinner, Carburetting apparatus. reported in page 152, AutoMotor Journal 3 February 1906
- ↑ 'Lilley & Skinner, The Times, Tuesday, Jun 02, 1896; pg. 14; Issue 34906
- ↑ Skinner-Union Carburettor Improvement. page 28, The Commercial Motor, 24 August 1920
- ↑ Profile Professor Herbert Skinner, The New Scientist 14 November 1957
- 1 2 James Leasor, Wheels to Fortune, Stratus, Cornwall 2001 ISBN 0755100476
- ↑ Colin Campbell, Tuning for Economy, Springer 1981 ISBN 9780412234903
- ↑ Nick Meikle, Malloch's Spitfire: The Story and Restoration of PK350, Casemate 2014 ISBN 9781612002521
- 1 2 Burnett, John (2012). SU Carburettor Company catalogue. Salisbury: Burlen Fuel Systems.
- 1 2 James Leasor, Wheels to Fortune, Stratus, Cornwall, 2001 ISBN 0-7551-0047-6
- ↑ Herbert Wakefield Banks Skinner. 1900-1960 H Jones, Biographical Memoirs of Fellows of the Royal Society 1960
- 1 2 Companies House company number 00318520
- ↑ Companies House company number 03285338
- ↑ SU technical pages
External links
- Burlen Fuel Systems - manufacturer of genuine SU carburetters
- A very comprehensive SU and Stromberg Carb Needle Selection and Analysis Tool
- Guide to setting up and tuning SU carburettors
- Classic Motorsports magazine's guide to understanding, tuning and rebuilding SUs